Cirrus3D
Cameras
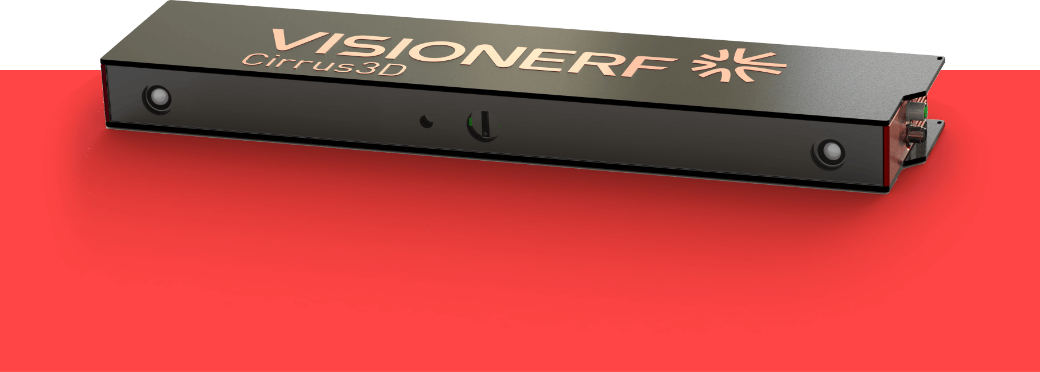
Made in
France by
The +
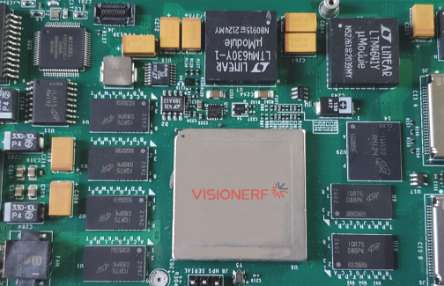
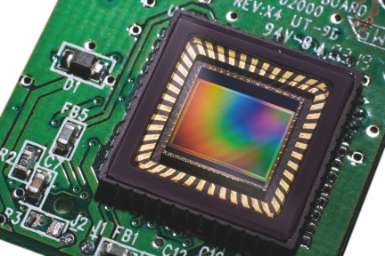
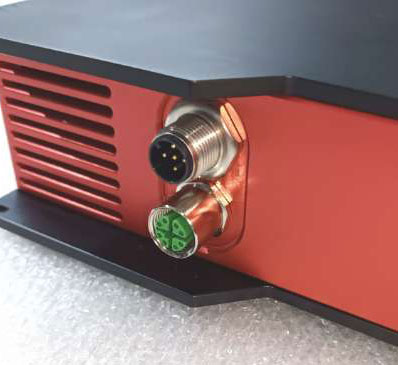
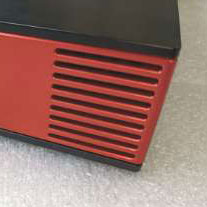
Why
Ever since the first-generation Cirrus3D camera launched in 2015, Visionerf has constantly improved its products to provide its customers with a high-end scanner capable of operating in the most demanding, dusty and humid environments such as foundries. The unique design of this camera, based on the principle of high-resolution stereoscopy, enables very small elements to be viewed with great precision in an extremely short time. Combined with powerful structured light, the quality of information remains constant on a wide range of materials. From black to high-gloss, measurement reliability remains at the highest level. The choice of top-of-the-range components contributes greatly to the robustness and reliability of these products. And Cirrus3D sensors can work with all cloud of points processing softwares on the market, either using the GigE/Genicam satndard protocol, or using our SDK (Software Development Kit) provided free of charge with each sensor.
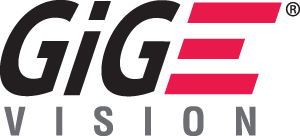
For
Today, our Visionerf 3D cameras are used in all sectors of activity, for precise handling of parts of all sizes (screws, mechanical body parts), for robot guidance in high-volume applications (from automatic detection of potential gas leaks on refrigerators to automatic changeover of drilling tools on giant tunnel boring machines), and for monitoring and inspecting products directly on production lines.
Our range of 3D cameras
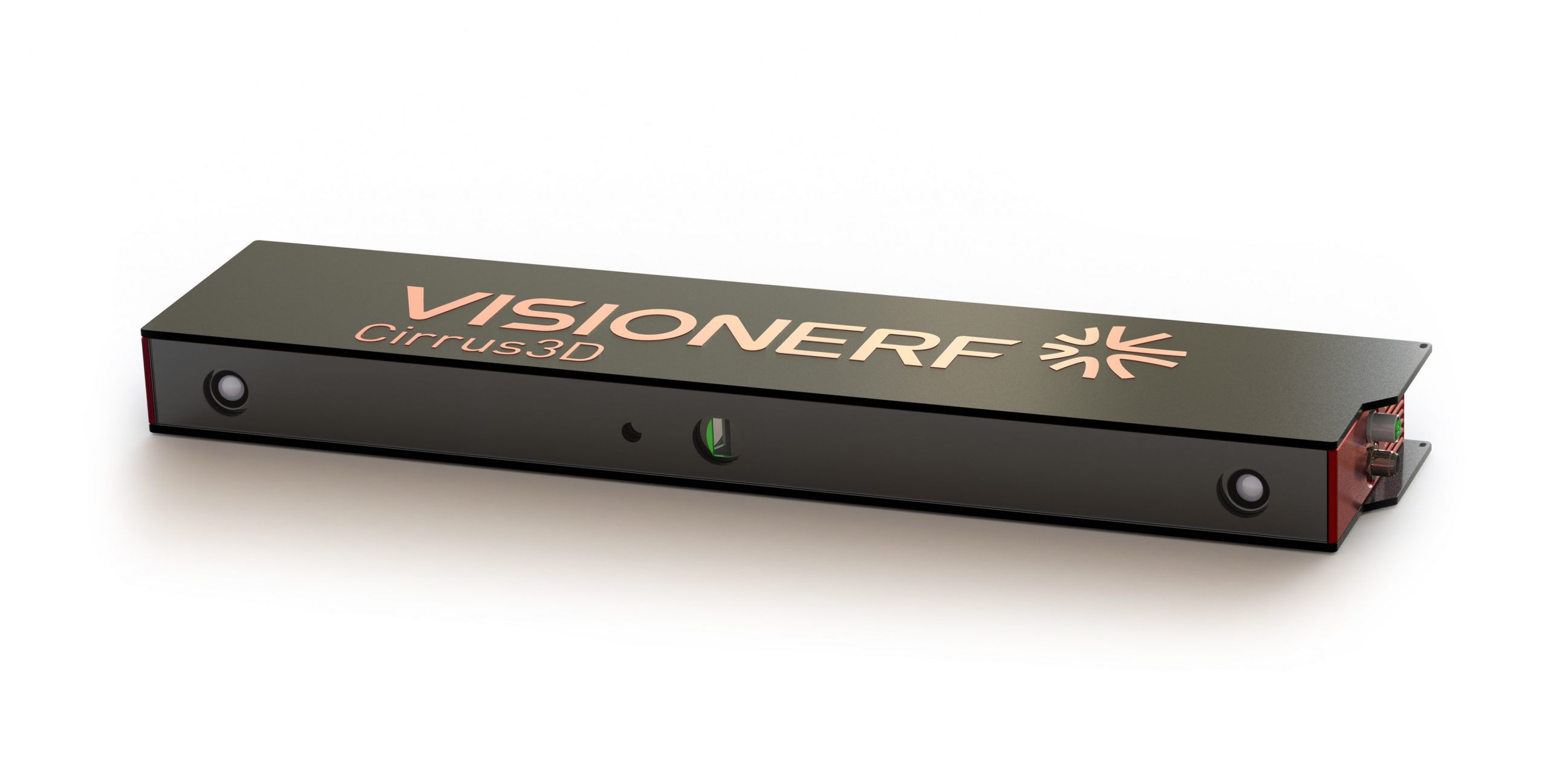
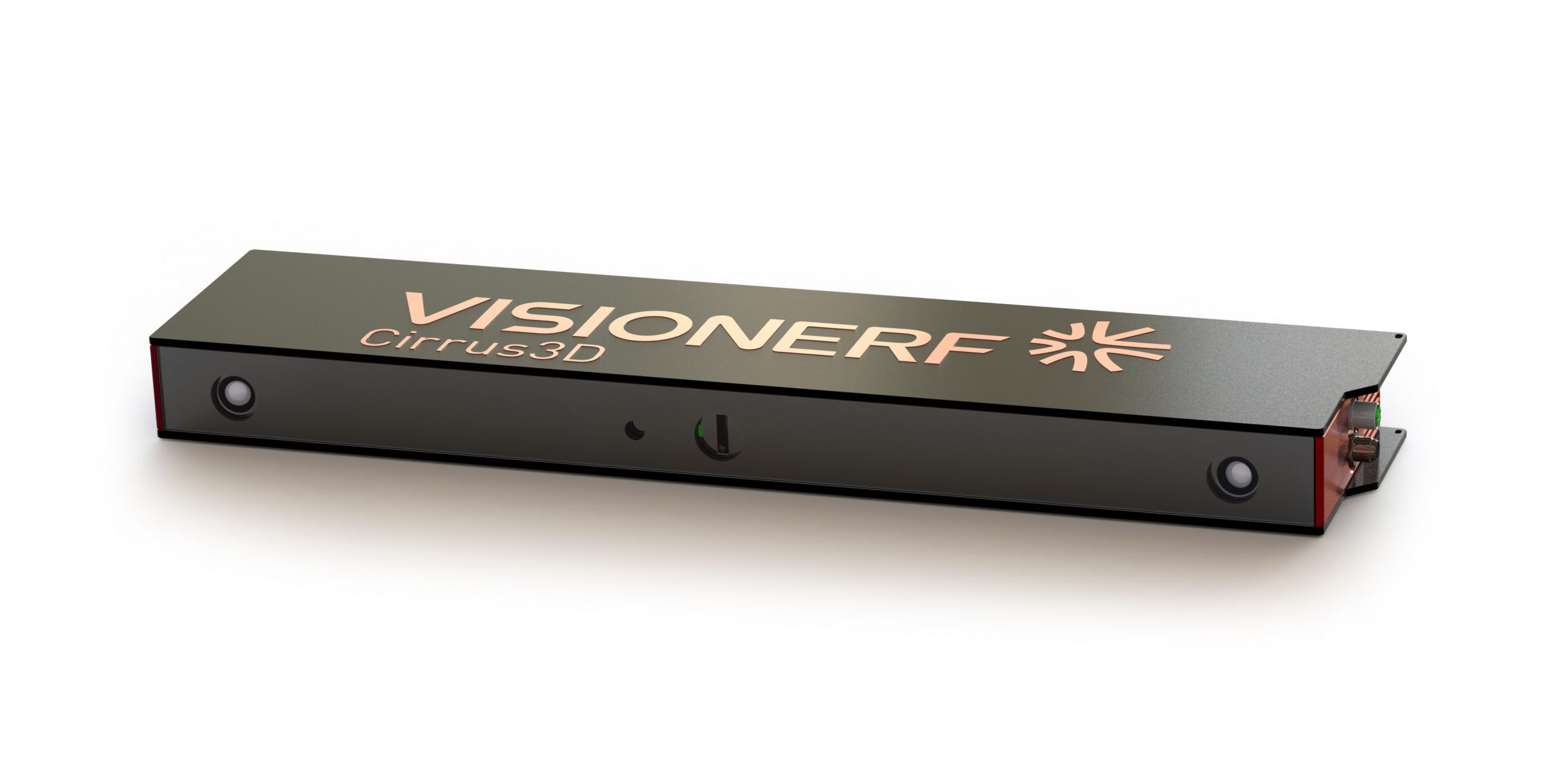
Sensor
Manager
"Sensor Manager" is the name of the software used to setup all parameters of the Cirrus3D sensors. It is simple to use and is available for Linux and Windows systems. If required, all parameters can also be adjusted without this software, using dedicated TCP/IP or GigE/Genicam commands.
There is no need to be an expert in vision or cameras to get beautiful cloud of points in just a few minutes.
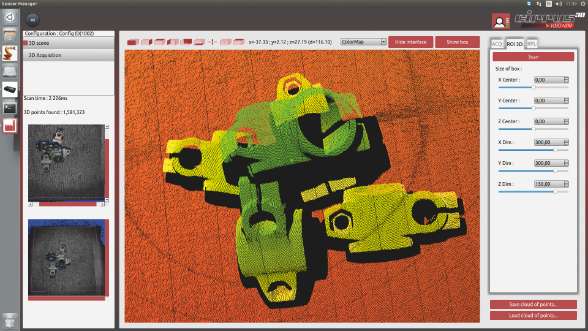
1. First, take a scan of your parts to get an initial idea.
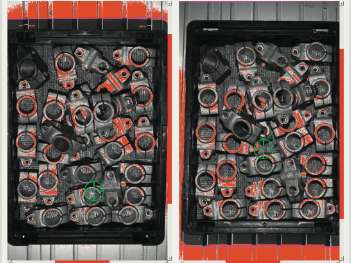
2. Then you can choose the cloud of points density and the sensor sensitivity.
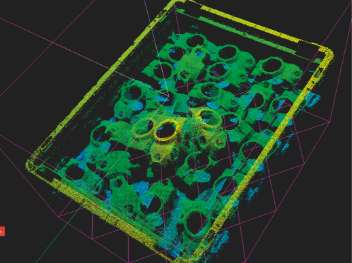
3. Finally, you cand adjust the working volume of the sensors to reduce the scan time.
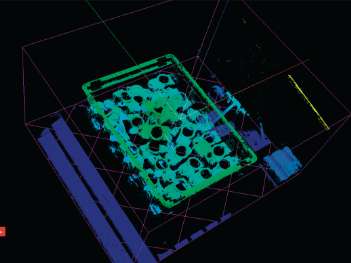