Bin
Picking
in real-time
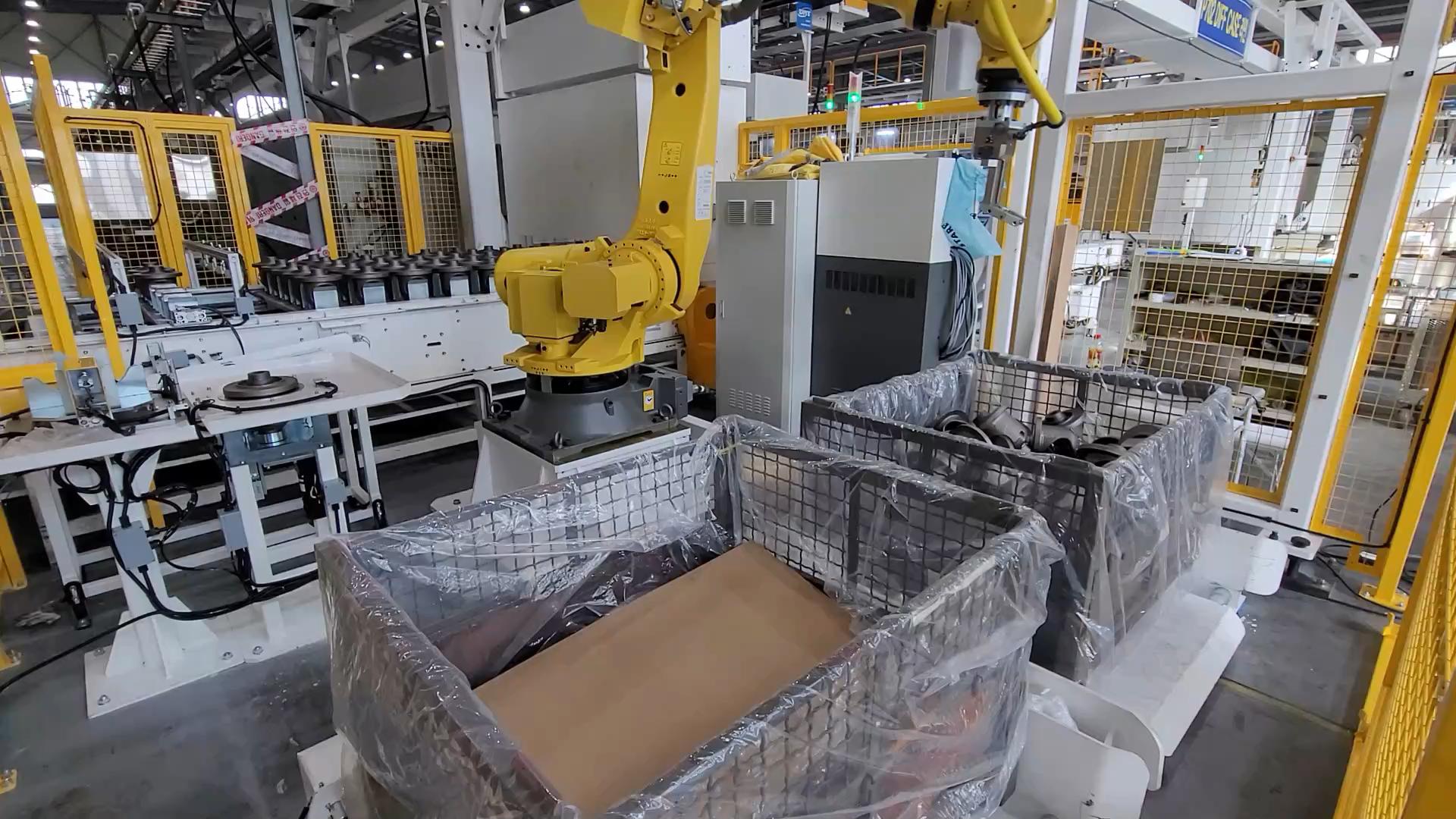
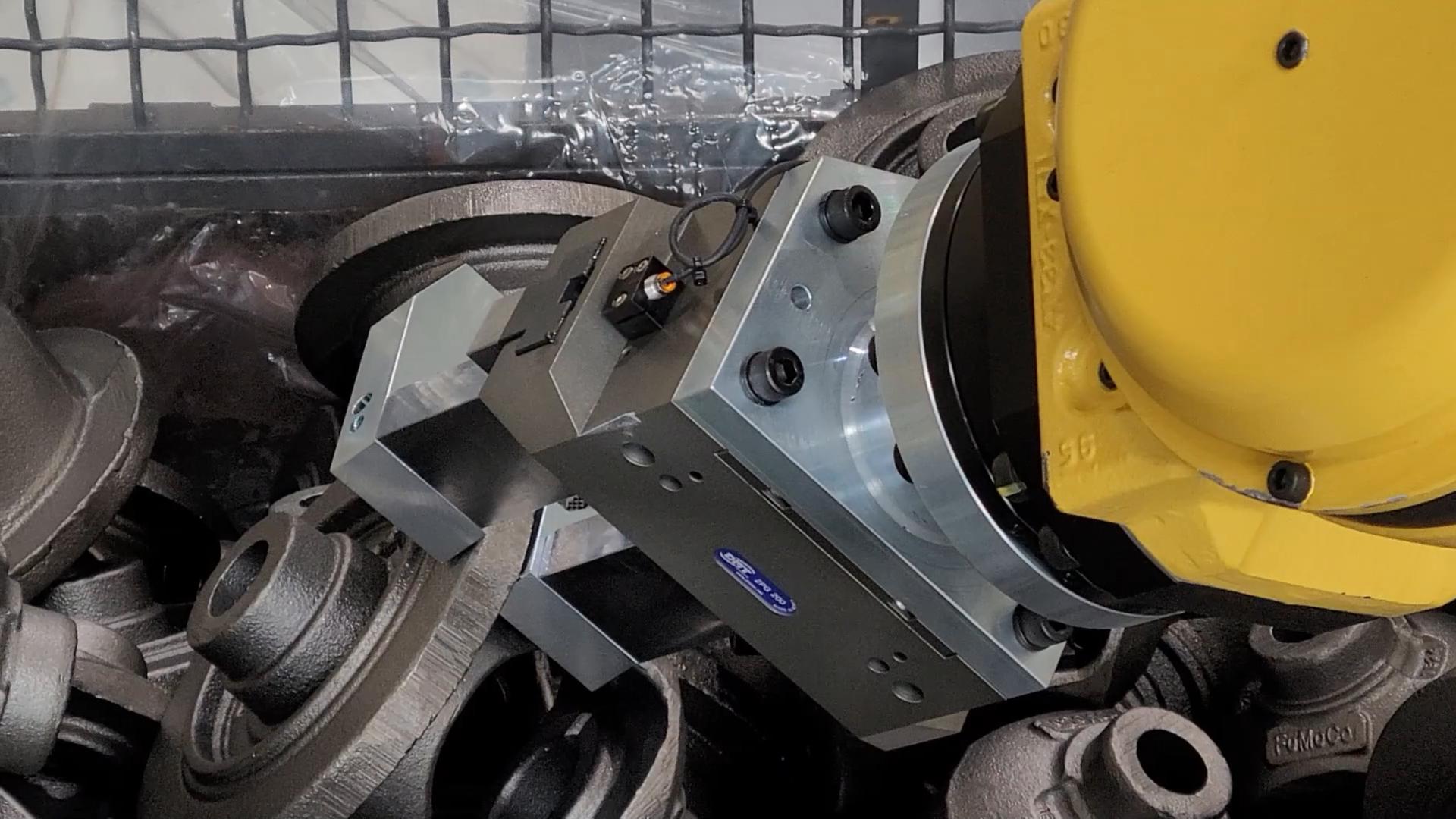
bin picking ?
- Automates picking tasks for even complex parts arranged in bulk, whether in rows or semi-rows
- Automates Pick and Place operations
- Guarantees a sustained and constant cadence (from 1 second per part entered, depending on the size of the robot, the general configuration and whether or not it scans in masked time...)
- Guarantees precise, repeatable positioning of captured parts (of 0.1 mm or 0.5 mm depending on part size)
- Guarantees that the gripper does not collide with the environment during gripping
- Avoids additional packaging costs
The bin picking process
The Cirrus3D performs bin picking by automatically detecting the shape of the part, or by comparing its CAD file with a set of 3D measurements taken on the scene. Point cloud processing locates parts in the scene and its environment, guaranteeing collision-free part picking. The robot receives the position of the part to be gripped in real time, and - element by element - empties the entire container to perform the ungripping operation.
A new CAD-free software variant enables faster implementation in some cases.
Step 1: 3D SCAN
From real to virtual
The Cirrus3D camera digitizes the actual work scene in the form of a 3D point cloud. The sensor uses stereovision technology for data acquisition, ensuring the quality of the information contained in the scan for maximum performance in scanning results. The user can graphically define the parameters of the bin picking scene: working volume, density of points contained in the point cloud, etc.
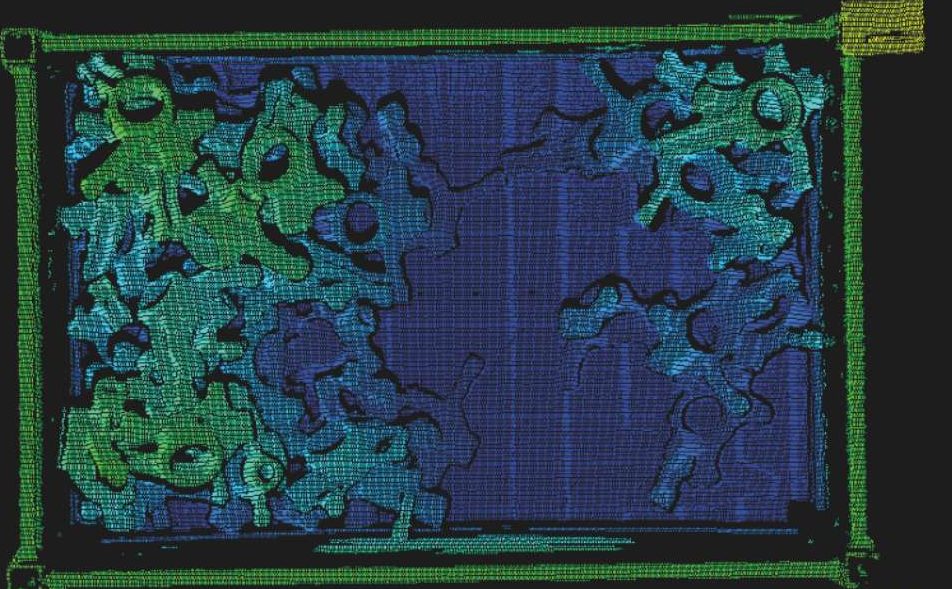
Step 2: LOCALIZATION
Locate and manage gripping
The image processing software locates the best part to grip based on its 3D measurements, by comparison with the CAD model of the part, or by automatically detecting its shape. To guarantee safe gripping, any overlap with other parts is simulated by building a virtual work scene.
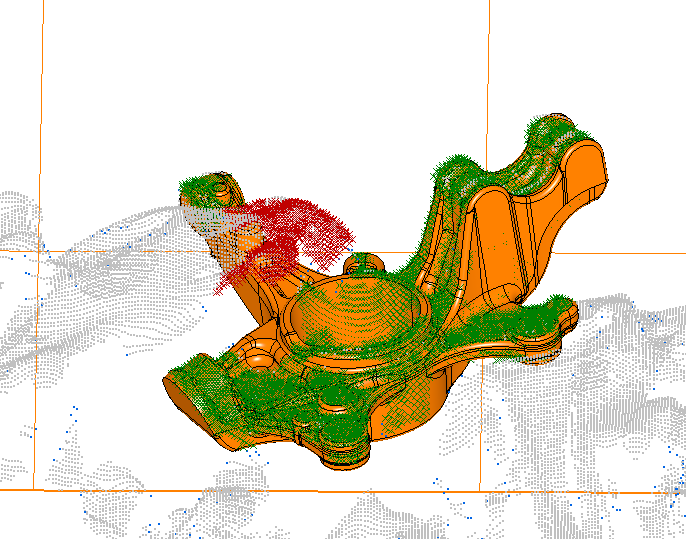
Step 3: GRIPPING
Gripper management and gripping points
Several grippers and pick-up points can be easily defined in the software for complete container emptying. An integrated simulation tool checks the design of mechanical elements (cell, robot, grippers) and the accessibility of gripping points.
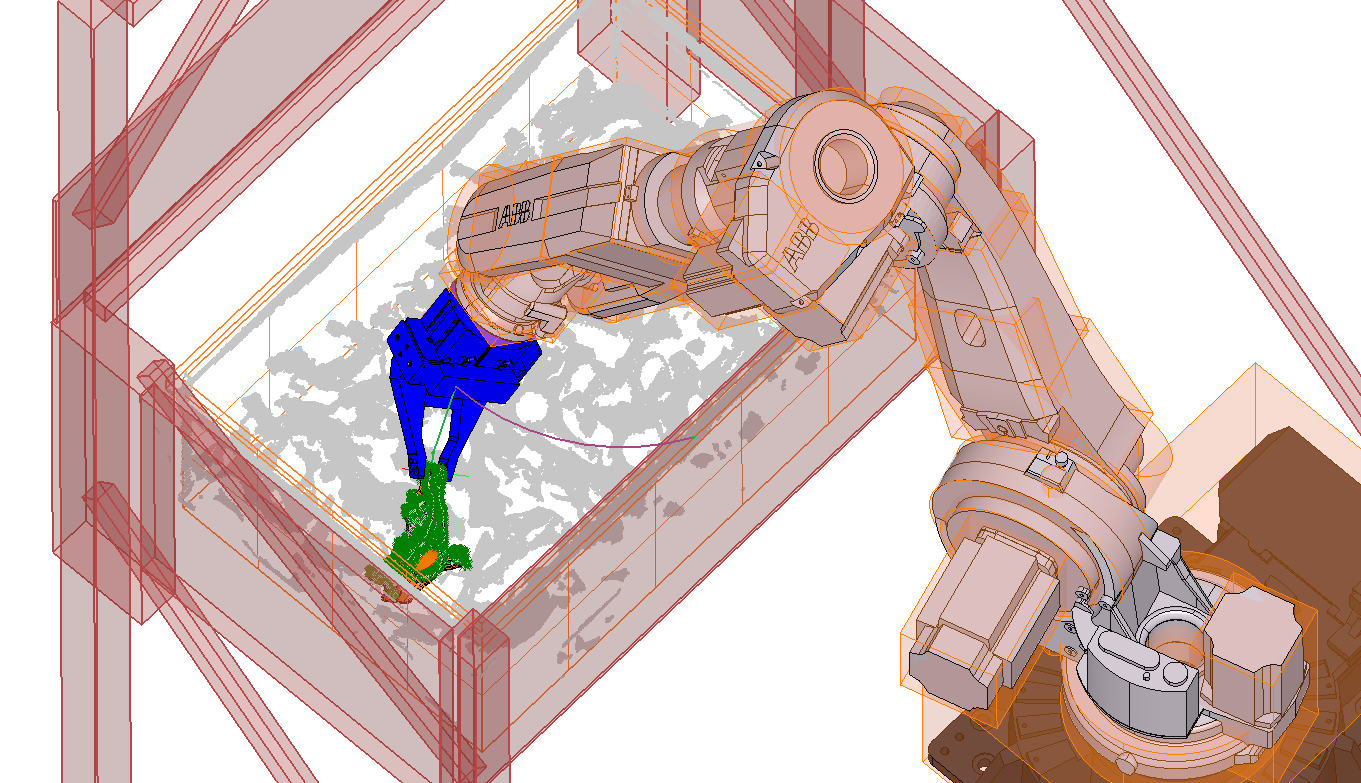
Step 4: ROBOT PATH PLANNING
Robot trajectory management
The Pick3D software calculates the optimal robot trajectory, whatever the make and model, to avoid any collision with the working environment. It transmits the angular positions of each axis to the robot controller, taking into account any singularities.
As a result, the robot application is easier to develop, and integration time is considerably reduced. In addition, collision management is better understood and more precise, enabling the robot to "dive" into the skip in complete safety.
In the end, this simpler and shorter integration, combined with a greater productivity, also guarantees a faster ROI.
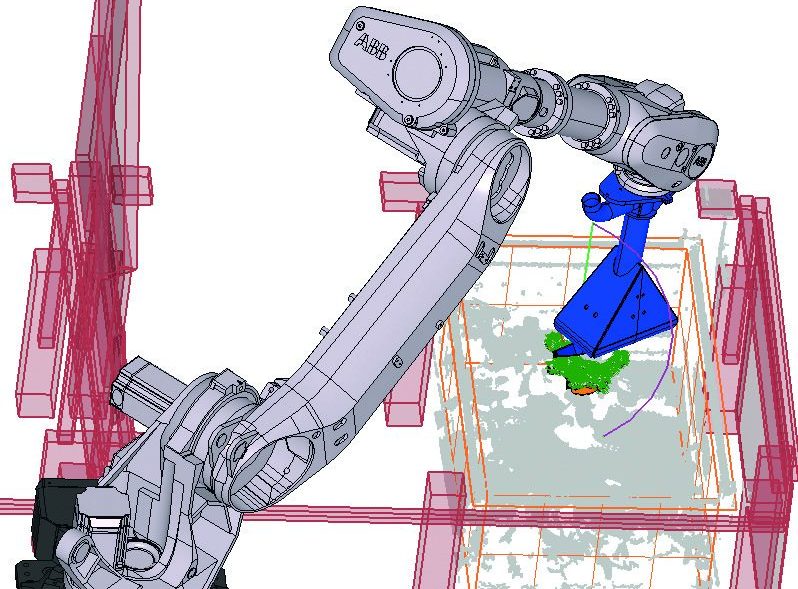
Part types
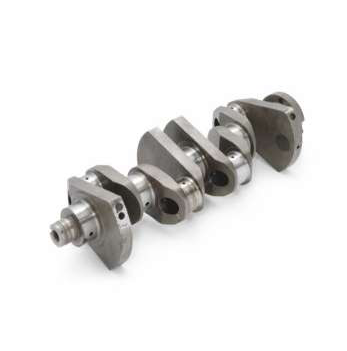
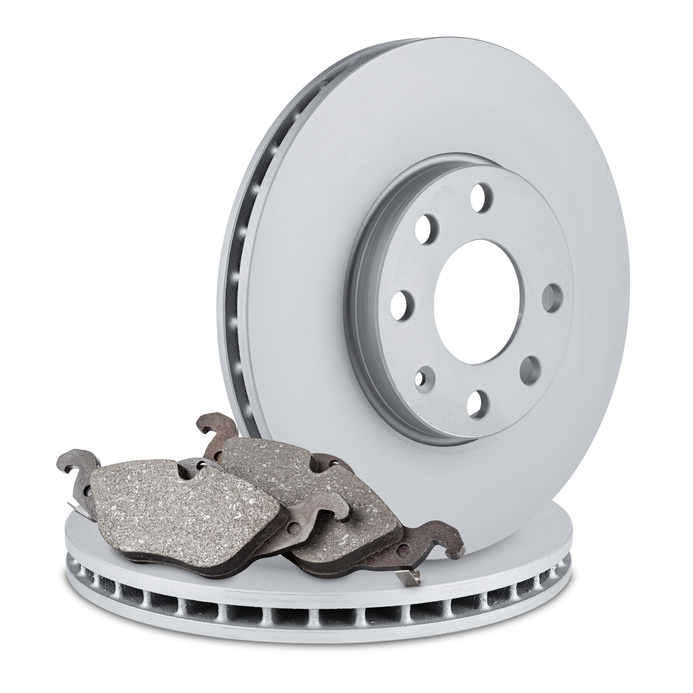
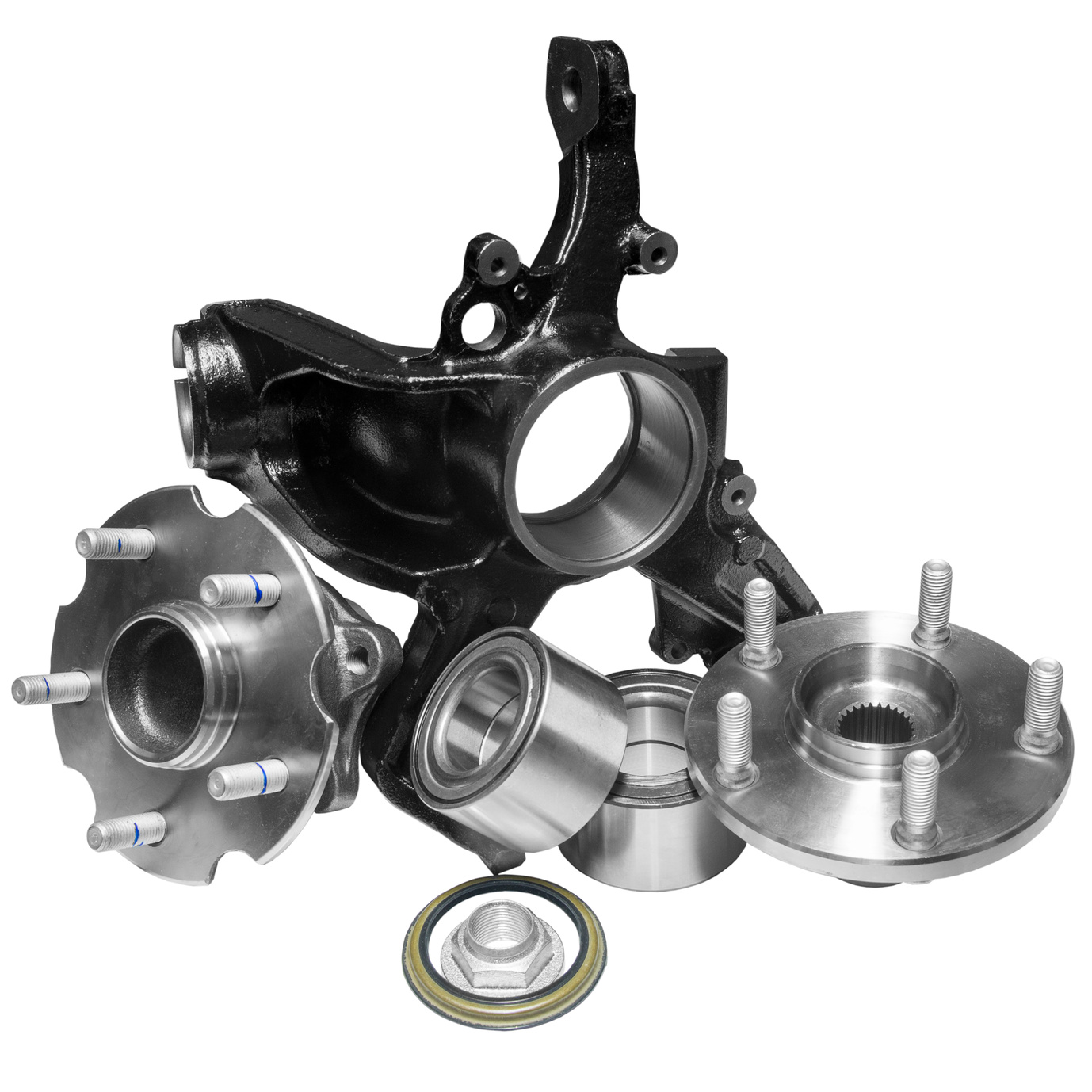
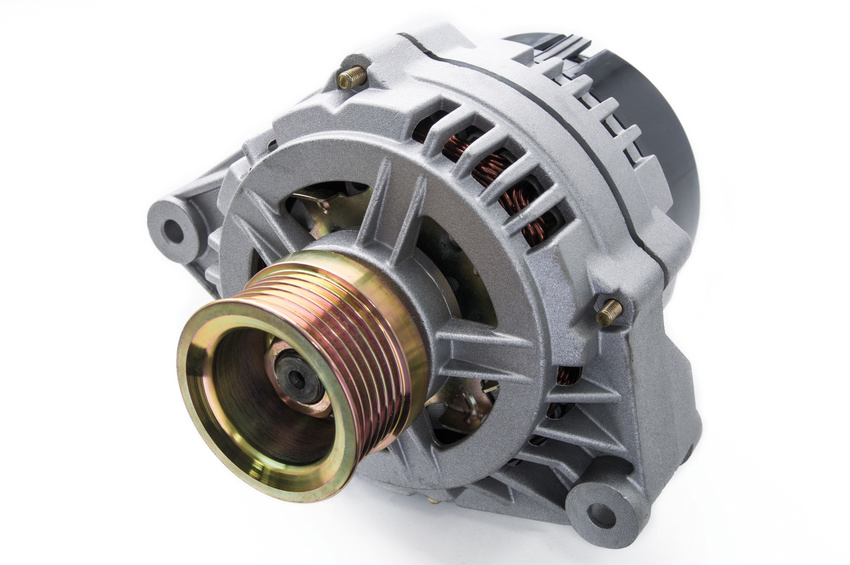
Why
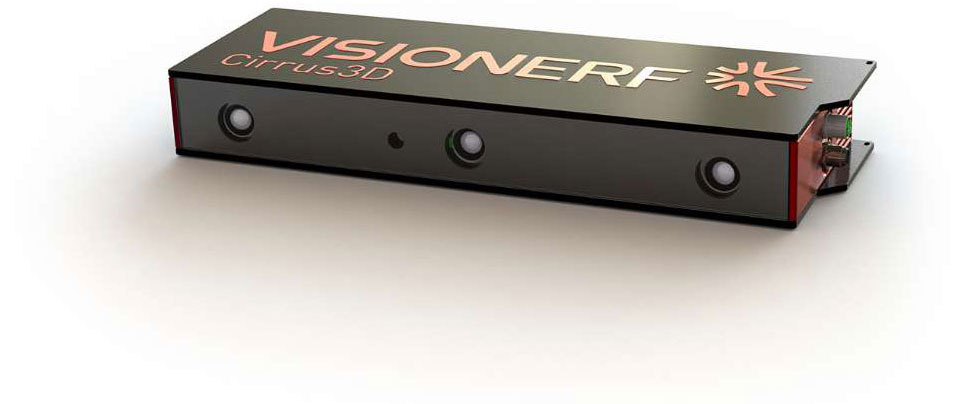
Since the first-generation Cirrus3D camera was launched in 2015, Visionerf has constantly improved its products to provide customers with a high-end scanner capable of operating in the harshest environments, such as foundries or dusty, humid environments.
The unique design of this camera, based on the principle of high-resolution stereoscopy, enables very small elements to be viewed with the utmost precision in the shortest possible time. Combined with powerful structured light, the quality of information remains constant over a wide range of materials. From black to high-gloss, measurement reliability remains flawless.
The choice of top-of-the-range components contributes greatly to the robustness and
reliability of our products.
Today, our cameras are used in all sectors of activity, for precise handling of parts of all sizes (screws, mechanical bodywork parts), for robot guidance in high-volume applications (from
automatic detection of potential gas leaks on refrigerators to automatic changeover of drilling tools on giant tunnel boring machines), and for monitoring and inspecting objects directly on production lines.