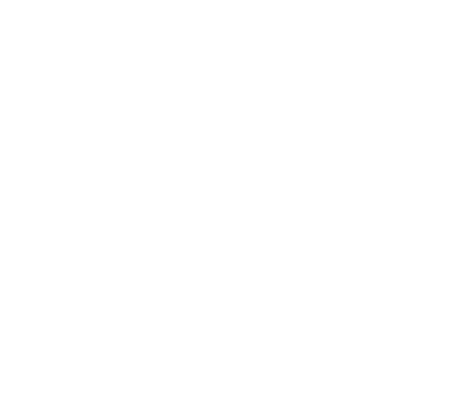
OPTICAL SORTING
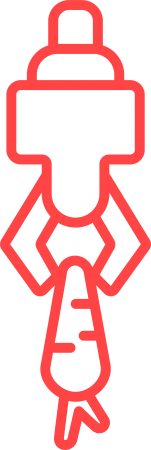
with a high reliability
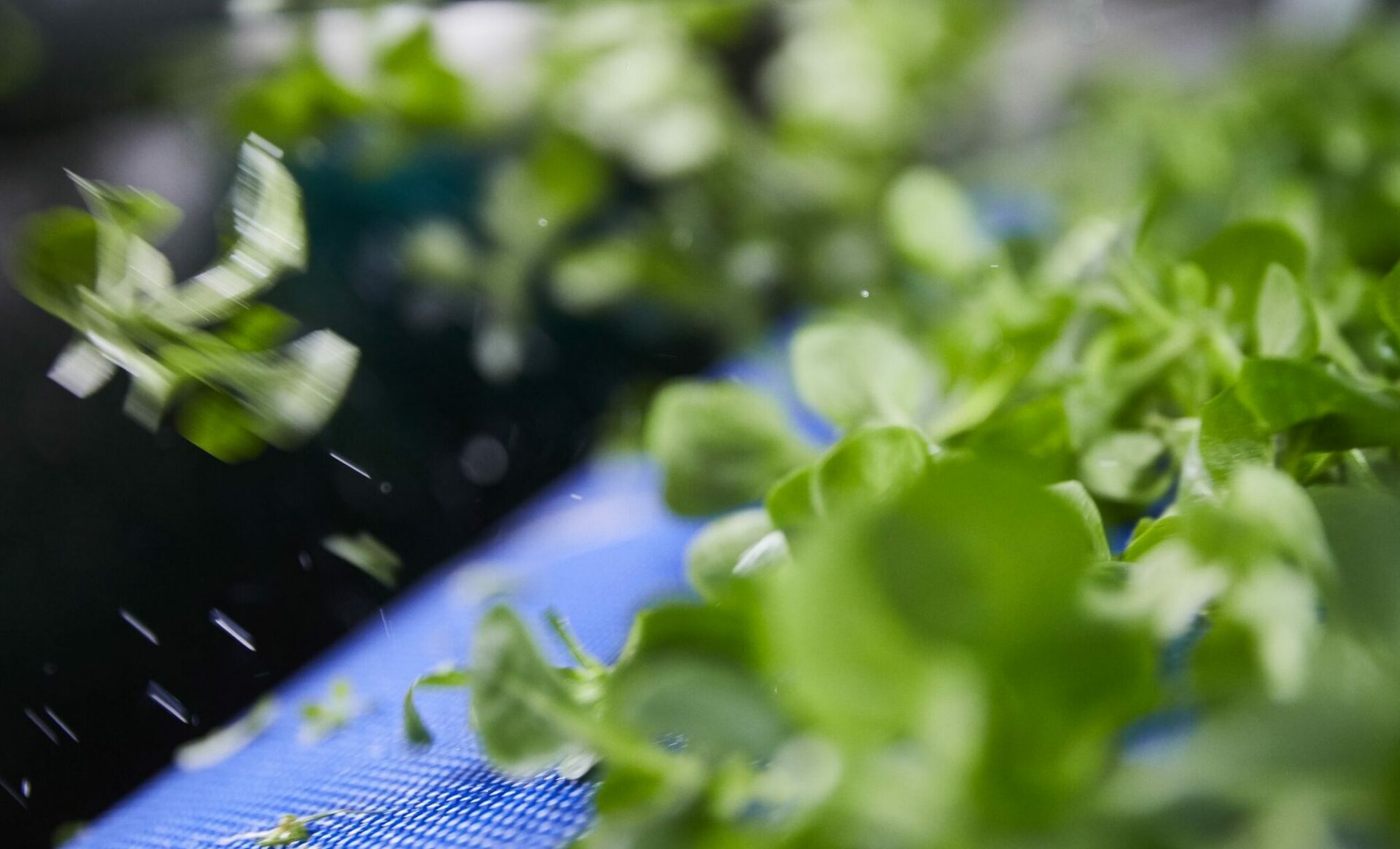
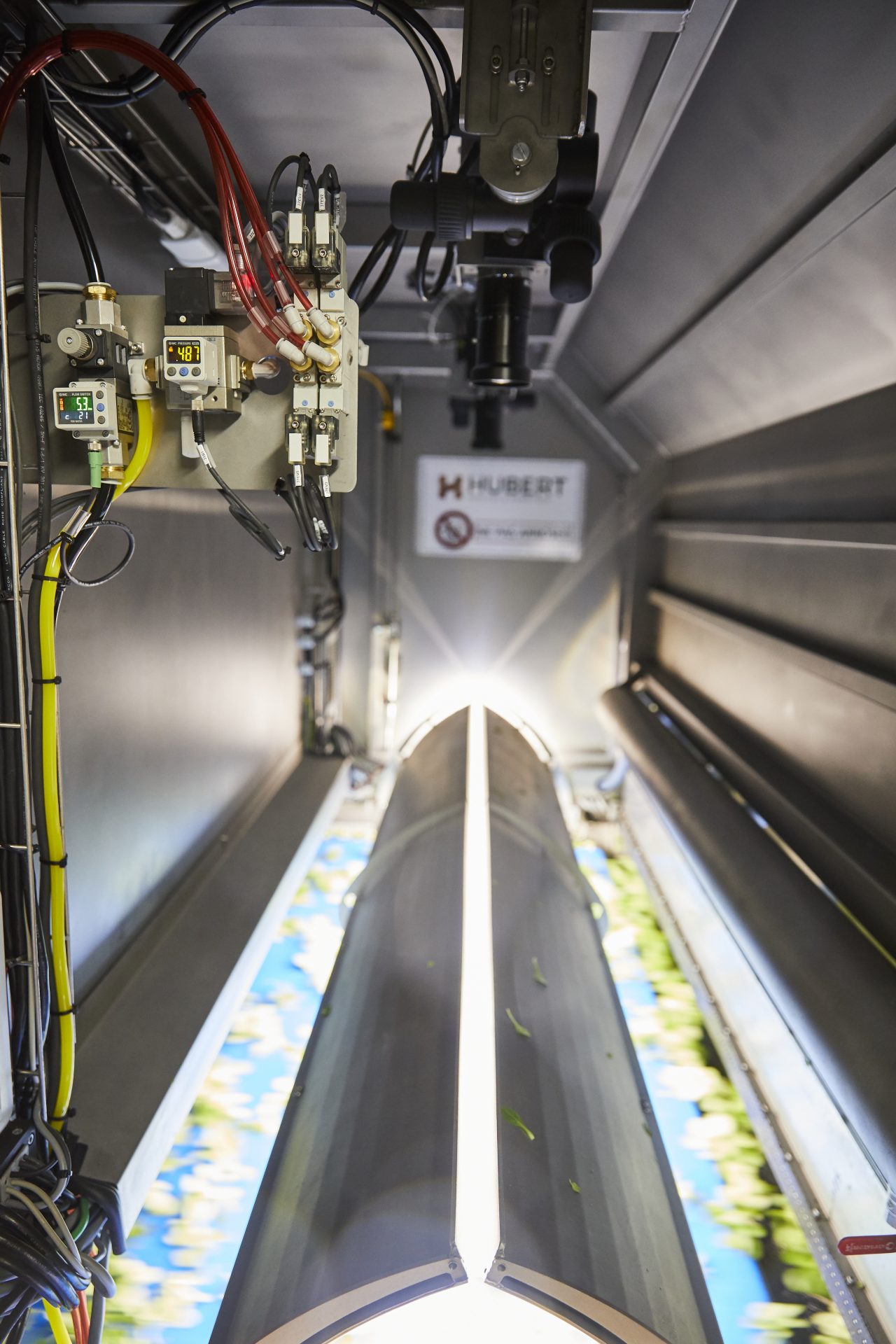
and so much more
Optimum return: the high quality of the components and the technology used enable advanced product analysis and extremely precise scrap ejection. This guarantees optimum efficiency, with a false scrap rate close to 0% and a true scrap rate close to 100%.
Extremely robust: the electronic architecture of the vision system ensures a long service life and a lower energy consumption than systems based on graphics cards.
Adaptability: all Visionerf systems are designed in conjunction with the integrator and the customer to offer a state-of-the-art solution adapted to the customer's specific sorting constraints.
Ease of use and flexibility: the software associated with the optical system features an intuitive interface with a simple set of cursors, enabling the customer to determine the desired level of sorting quality.
Responsive technical support: the machine's main settings are made in the factory according to the specifications defined with the customer. Installation, parameter fine-tuning and training are carried out on site by the integrator and Visionerf. Remote technical support is provided: a Visionerf expert can take control of the software (secure data) at any time and assist the customer without wasting time.
Maintenance: the optical system requires no special maintenance.
A SOLUTION ADAPTED
Visionerf's image processing systems are designed to adapt to the complexity of the product to be sorted (shape, color, gloss, etc.) and to the level of final quality required by the customer, using 2D or 3D sensors and optics with or without infra-red.
Visionerf's vision systems use unique processes based on the principle of stereoscopy, in order to meet the requirements of certain food sorting applications, such as shellfish, in terms of ejection precision. This cutting-edge technology uses two cameras and guarantees high reliability and precision by exploiting the redundancy and consistency of results.
A PERFECTLY CONTROLLED PROCESS
From image capture to ejection
Visionerf has developed a vision controller specifically for image acquisition and processing on high-speed products.
Its unique technology, based on an specific processor, enables images to be captured and analyzed on a conveyor at speeds of up to 3 m/s.
The result is then transmitted in real time to 1 or more ejectors (compressed air, mechanical) for remarkably efficient sorting.
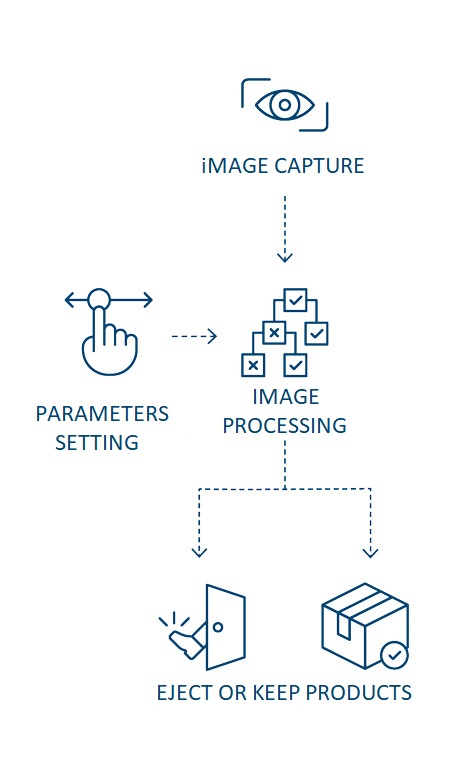
A MULTI-SENSOR SOLUTION
With high-end 2D and 3D
In the case of certain products with awkward shapes, a high-end 2D color line-scan camera is used to eliminate parallax errors. Special LED lighting is positioned beneath the sensors. The projected light is precisely redirected by a dome onto the scanned area of the product. The combination of a color camera sensitive to red, green, blue and near infrared - a 3D stereo camera - and LED lighting provides high-resolution information on the product, and detects even the smallest foreign bodies (of the order of 1 mm²), as well as stained products that do not conform (damaged or diseased).
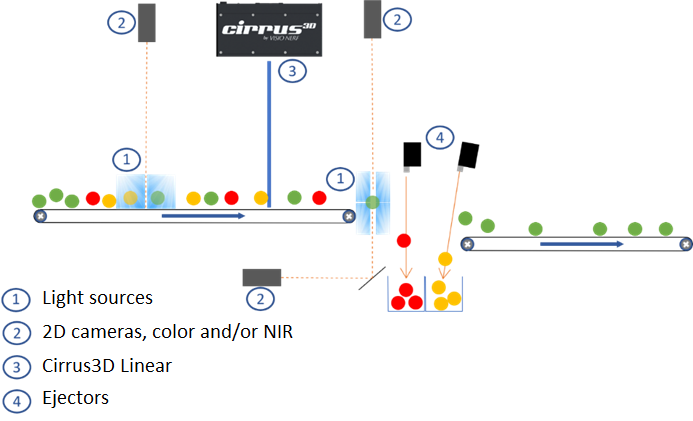
SORT BY COLOR, SHAPE, SIZE
With maximum efficiency
The user has the option of grading the sorting process according to the objective he wishes to achieve and the initial quality of the harvest. The user can choose to eliminate foreign bodies, vegetation (stalks, petioles, etc.), immature berries, berries with rot, crushed berries, candied berries, etc. He can adjust the parameters to adapt the sorting level to his requirements.
Different settings are available, based on :
Color (to eliminate immature green or pink berries),
Size (e.g. elimination of verjuice, stalks, etc.),
Object shape (e.g. eliminating crushed kernels with shapes other than round, healthy ones).
Once the program has been adjusted, and following dedicated image processing, each element passing in front of the camera is analyzed and either eliminated or retained.
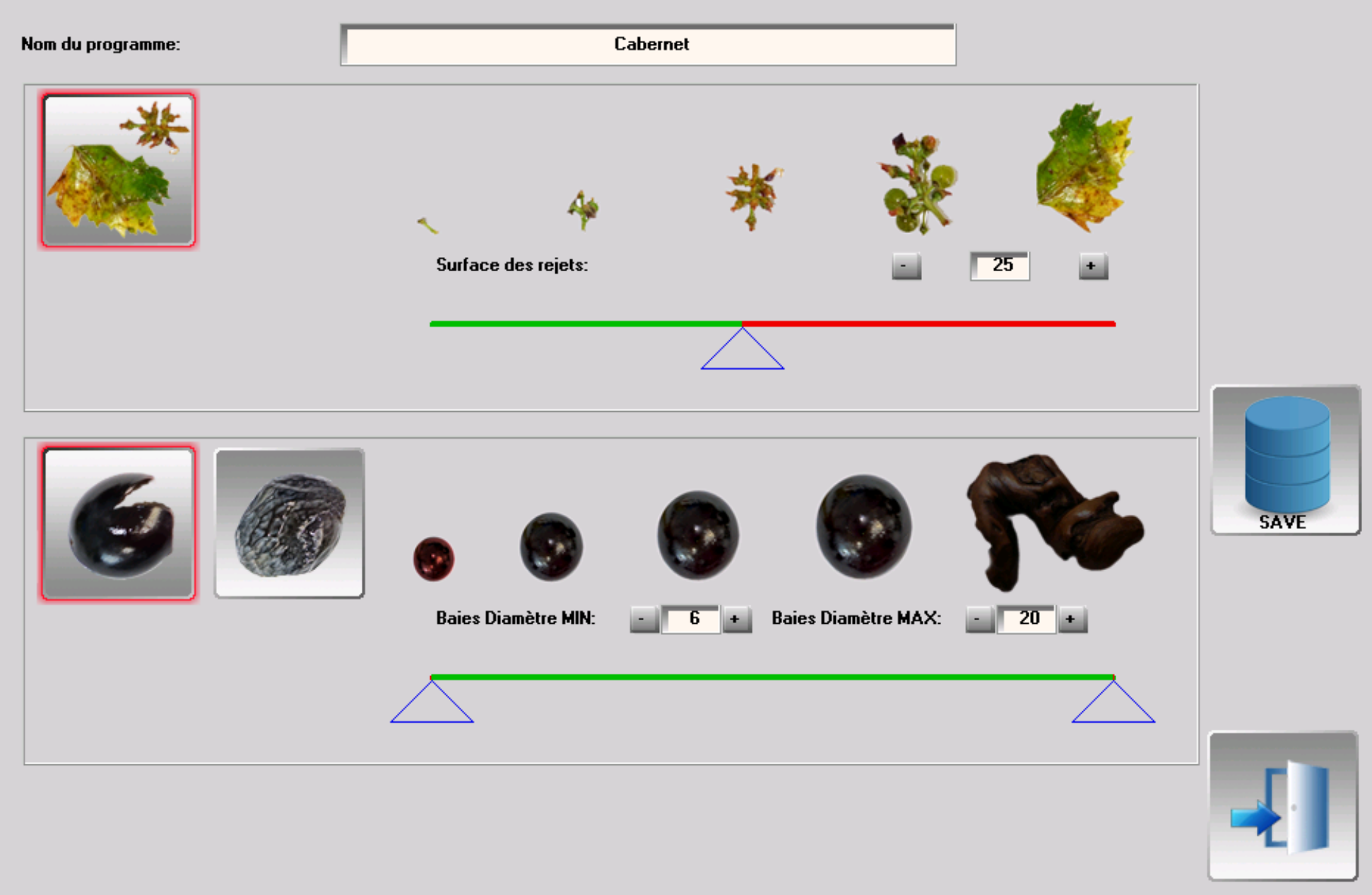
A SIMPLE AND ADAPTABLE INTERFACE
For a quick and smooth launch
An easy-to-use, intuitive interface allows the operator to manage all the parameters required to operate the sorting machine (belt speed, vision and ejection systems, automatic cleaning cycle, etc.). The operator can save up to 16 programs, for which he can define the appropriate parameters to the quality of the batch to be sorted. The software also provides statistics on the use of the optical sorter, such as estimated throughput or ejection rate.
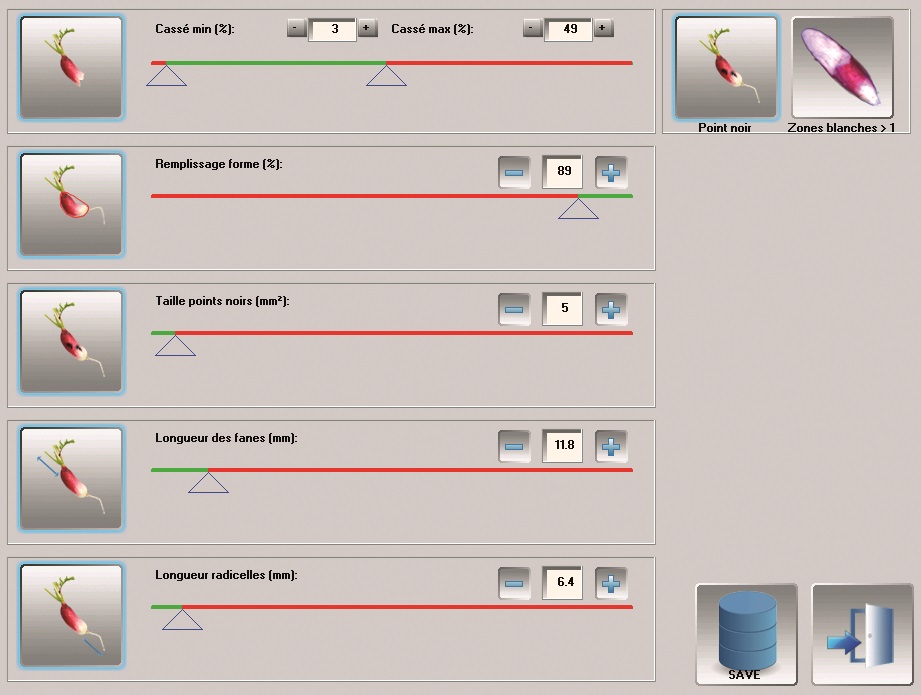
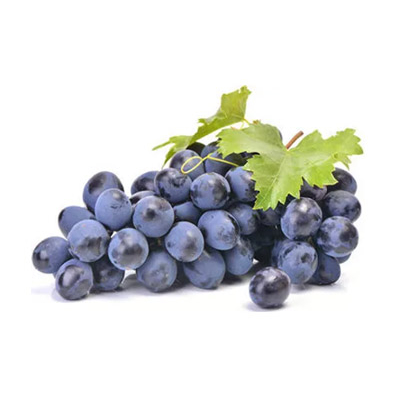
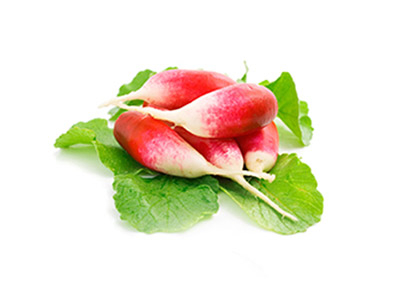
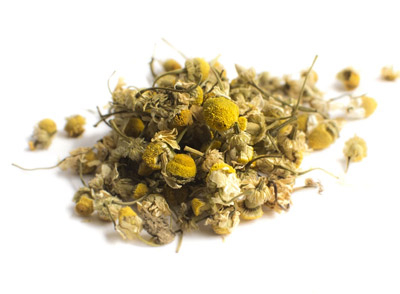
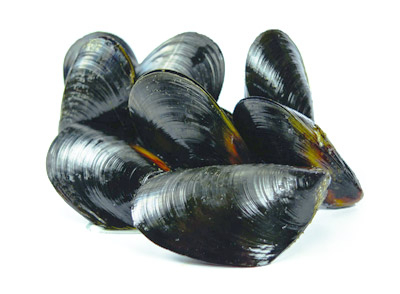
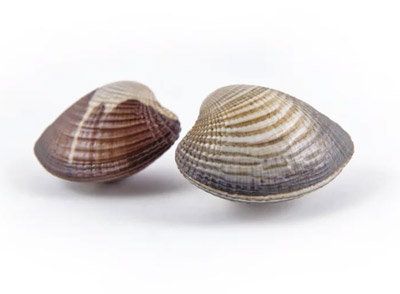
Why
Since the first-generation Cirrus3D camera was launched in 2015, Visionerf has constantly improved its products to provide customers with a high-end scanner capable of operating in the harshest environments, such as foundries or dusty, humid environments.
The unique design of this camera, based on the principle of high-resolution stereoscopy, enables very small elements to be viewed with the utmost precision in the shortest possible time. Combined with powerful structured light, the quality of the information remains constant across a wide range of materials. From black to high-gloss, measurement reliability remains impeccably high.
The choice of top-of-the-range components contributes greatly to the robustness and reliability of our products.
Today, our cameras are used in all sectors of activity, for precise handling of parts of all sizes (screws, mechanical bodywork parts), for robot guidance in high-volume applications (from automatic detection of potential gas leaks on refrigerators to automatic changeover of drilling tools on giant tunnel boring machines), and for monitoring and inspecting objects directly on production lines.