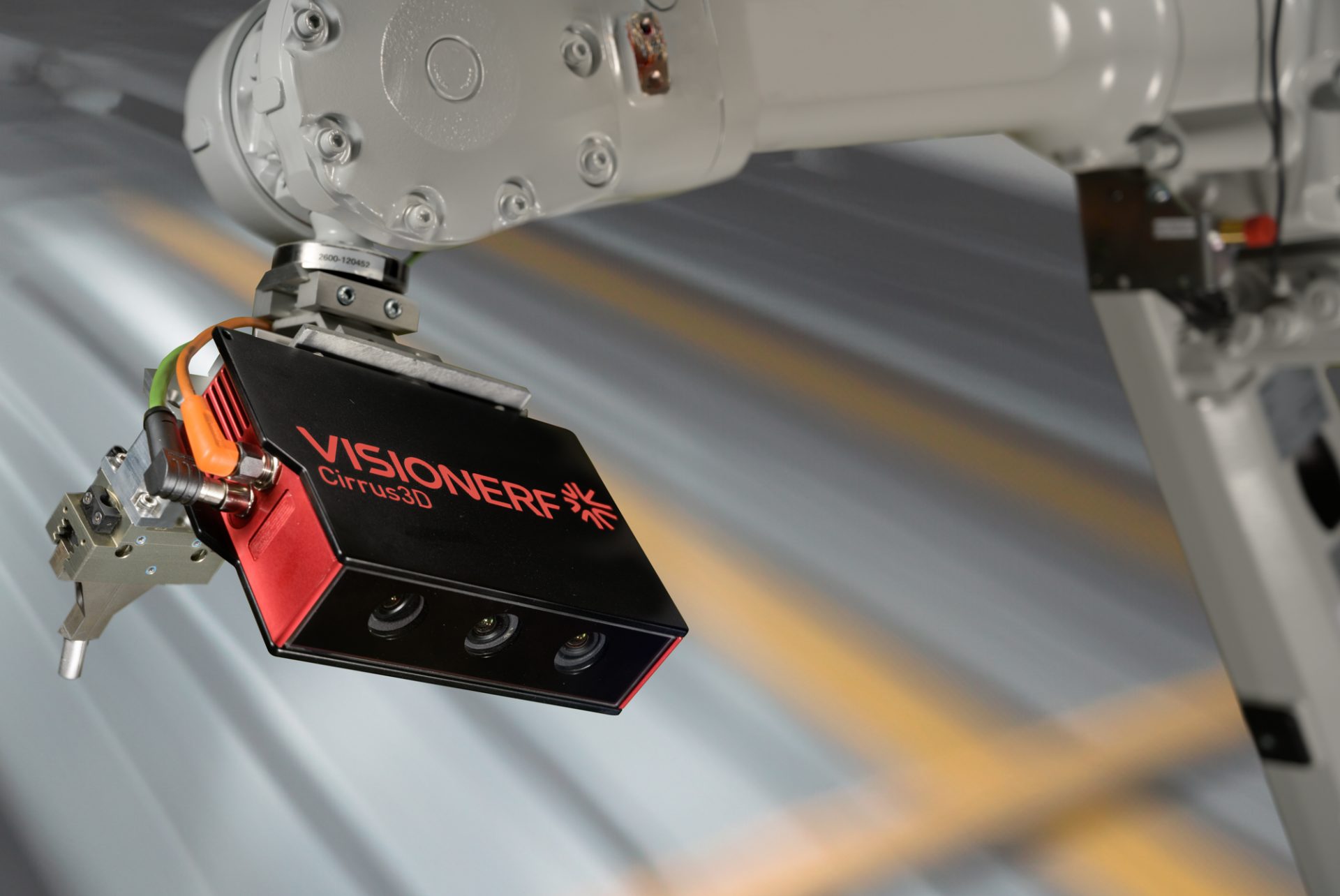
Awareness is Power
"The more you see, the more you know, the better you produce" For over 30 years, we have been creating and developping image processing hardware and 3D cameras for industrial use all around the world. Our customers may be end users, but are usually machine builders or integrators. Our constant focus is to help our customers to get the right automation solution they need. We enjoy to empower them by using appropriate vision solutions.
Discover our 3D cameras
Cirrus3D
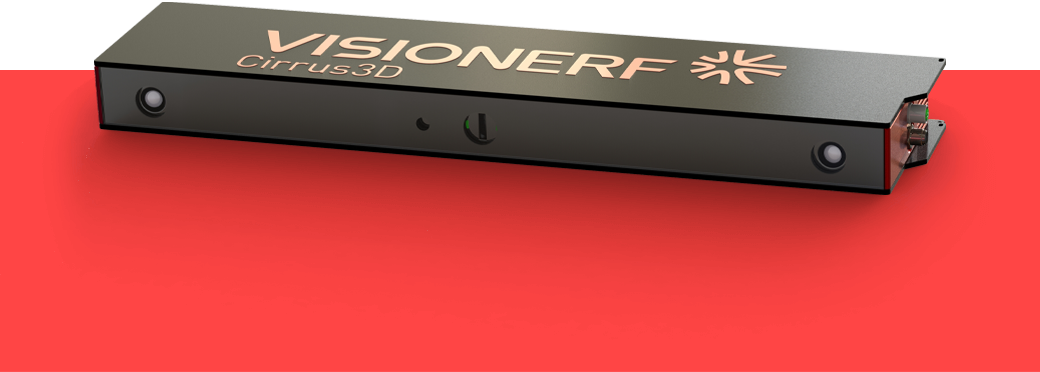
Our Cirrus3D cameras are ready to use in your vision system or your production line. Used as a fixed or mobile 3D sensor, the Cirrus3D enables vision and robotics applications of incomparable efficiency and very high quality. Dedicated to industrial use, Cirrus3D scanners are not sensitive to the environment: dust, dirt, ambiant light, product color changes. With our Cirrus3D sensor, you can forget all the usual camera-related troubles: no more lens adjustment, no more light design, no more calibration. The Cirrus3D is really ready to use and provides a calibrated cloud of points in mm, right out of the box.
Find out more
OUR
APPLICATIONS
Our products are suitable for a multitude of applications. Whether it's quick and easy location of your raw or finished parts, automation of precision operations on products with unknown shape or positioning, performing an uprooting operation, identifying a part or checking the conformity of production parts, the cirrus3D range takes care of it all, while providing an excellent return on investment. And our 3D sensors are compatible with all processing softwares, either through GigE vision / Genicam protocol or by using our SDK.

YOUR
NEEDS
We're with you every step of the way, working with you to develop a product or solution that's perfectly suited to your needs. You can count on us to provide you with a sensor adapted to your installation and which integrates perfectly with your existing solution, or to customize our offer for a unique product that's just like you.
Customer
testimonials
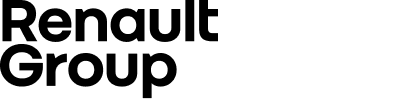
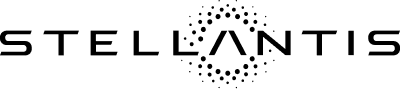
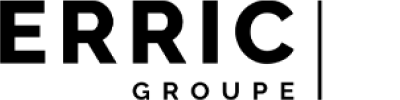
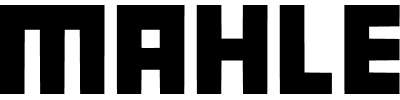